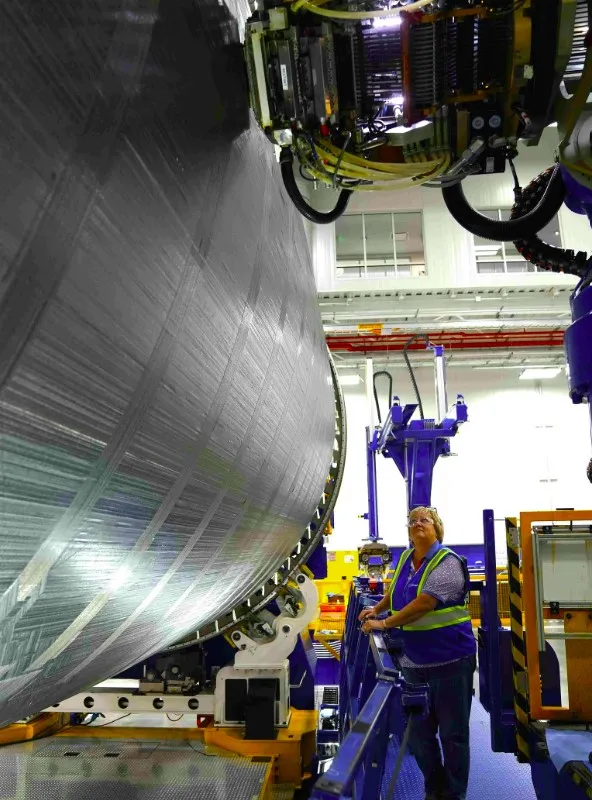
Above, Boeing Technical Fellow Karin Anderson checks the carbon fiber tape dispensing system of an automated fiber placement machine at Boeing South Carolina.
(Boeing | Kaitlin Stansell photo)
Twenty years ago, Boeing engineers predicted the use of composite materials in the design of the 787 Dreamliner would improve efficiency, durability, and even passenger comfort. Seeing the results after more than a decade in service, Boeing Technical Fellows count the promises made as promises kept.
Catch up quick: Boeing’s introduction of the 787 Dreamliner in 2004 signaled a significant departure from traditional commercial airplane manufacturing. With an airframe comprised of 50% carbon fiber reinforced plastic and other composites, the 787 entered history as the Boeing commercial airplane with the most extensive use of composite materials.
Why it matters: According to 787 Chief Engineer John Murphy, composite materials reduce airplane weight and provide aerodynamic benefits, contributing to the 787 Dreamliner being up to 25% more fuel-efficient than previous-generation airplanes. Since entering service in 2011, the 787 has avoided more than 170 billion pounds (77 billion kilograms) of carbon emissions.
Composites offer several advantages over traditional materials:
- High strength-to-weight ratio: Composites are often stronger than steel yet lighter than aluminum, making them ideal for airplane construction.
- Corrosion resistance: Unlike metals, composites do not corrode, enhancing durability, especially in harsh environments.
- Fatigue resistance: Composites can endure cyclic stresses without degradation, improving the life span of the airplane.
- Design flexibility: Composites can be molded into complex shapes, allowing for more innovative and efficient structures.
What’s next: The 787 has demonstrated the efficiency and quality of several advanced manufacturing techniques, including the use of automated fiber placement machines in fabricating fuselage sections. But there’s still more to learn to optimize producibility of composite parts.
How it’s done: Watch a machine layer carbon fiber tape to build the aftbody sections of the 787 Dreamliner fuselage. This video has natural sound only. (Boeing video)
players.brightcove.net/800000612001/default_default/index.html?videoId=6359577036112
“With a clear engineering focus on improving producibility, we’re documenting our best design practices to capture the lessons learned and understand the reasons for the approaches taken for using composites on the 787, the 777X wing and other products,” said Boeing Technical Fellow Karin Anderson.
“Additionally, there is a lot of work being done to improve Boeing’s analysis tools, including investments in smart testing, artificial intelligence and machine learning,” said Anderson. “We want to refine requirements for Boeing’s future products, and we know composites will be part of that future.”
Learn more: Go inside Innovation Quarterly to discover more about composites and the 787 Dreamliner.
By Kaitlin Stansell
Be the first to comment on "The 787 Dreamliner Difference"